Tyre Pyrolysis Machine – Environmentally and Economically Way To Recycle Tyres
The world’s population is increasing rapidly resulting in increased environmental degradation from both industrial and human actions. This degradation demands continued waste management to reduce the piling up. An example is damping of worn-out tyres which has resulted in increasing heaps in town outskirts. These heaps continue increasing daily due to increased demand for cars. So how do we reduce these tyre piles? The answer is through pyrolysis.
What is pyrolysis?
Pyrolysis is the process of decomposing the tyres at very high temperatures without oxygen. This process offers both an environmentally and economically attractive venture. Find high quality of tyre pyrolysis plant for sale here.
Tyre Pyrolysis Process
The process initially involves shredding or halving the tyres to reduce the processing time taken to break down the batch by increasing the surface area to be heat reacted on. Shredding also increases the number of tyres that can be accommodated in the reactor. In some plants, the tyres are processed as wholes.
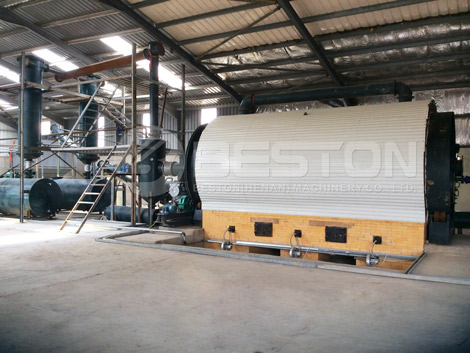
Tyre Pyrolysis Plant For Sale
The reactor
The next stage is the reactor which is oxygen free atmosphere which has a heating source or furnace. The amount of space left in the reactor after filling with the shreds should be approximately a third (1/3) of the total space to allow gas expansion. The reactor is slowly heated up by burning fuel such as charcoal, wood or natural gas up to temperatures above 1000 Celsius.
The reactor contains one main entry for the shreds and two exits; one to the condenser and the other for the ashes. Once the right temperature is achieved, the rubber polymers degenerate into small molecules which evaporate and exit to the condenser. Click here to know more about small scale pyrolysis plant.
During heating, it is necessary to understand that the heating rate is most crucial and affects the reaction time, the product yield, the product quality and the amount of energy required for the process. If the temperature is maintained at four hundred and fifty degrees, the main product will be a mixture of hydrocarbons. At temperatures above seven hundred and fifty degrees (750 ), there is the production of synthetic gas which is a mixture of hydrogen and carbon monoxide. The synthetic or syn gas can be used to further crack the liquids or used to heat up the reactor since it is flammable.
Once the rubber is fully burnt, the ashes known as char containing the steel wires are collected at the bottom. The combined solid product is then passed through a magnetic separator to attract the steel leaving the carbon black powder.
The condenser
Part of the condenser is a fractional column or a manifold that is used for heavy fractioning. Heavy fractioning involves the elimination of heavy fluids that may cause pipe blockage. This heavy oil flows to its own tank at the bottom while the lighter gases proceed to the condenser.
The condensing process involves external cooling by use of water resulting into the lighter gases becoming liquid in nature .the oil is then stored in tanks while the non-condensable gas is then desulphurized and dusted by the hydro seal and is thee used back in the furnace resulting in energy efficiency.
Types of pyrolysis plants
There are three types of tyre pyrolysis plants mainly the batch operating, semiautomatic and fully continuous operating plants. Batch operating plants are mostly manually operated and require more labour force as compared to the semi and fully continuous pyrolysis oil plant.
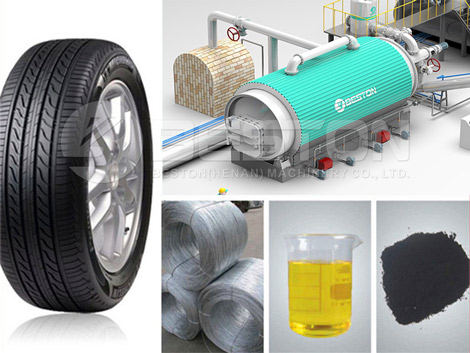
Tire to Oil Machine
Uses of tyre pyrolysis products
The products of tyre pyrolysis are steel wire, char or carbon black and pyrolysis oil. Pyrolysis oil is the main byproduct of the process having 45-50 %. It is of high calorific value and low ash, sulfur and carbon residual content hence making it suitable for cement kilns, paper mills, power plants and industrial furnaces.
Carbon black or char produced is about 30 to 35 %. It is used in the pigmentation and reinforcing phases during the tyre manufacturing process. It is also used to conduct away heat away from tyre threads reducing thermal damage resulting in increased tyre life. Other uses of carbon black go into the making of belts, gaskets, ink pigments and are also used in making radar absorbent material and ultraviolet radiation absorption.
The steel produced is around 15-25% of the by-product and can be recycled and used by steel rolling mills.
In conclusion, the tyre pyrolysis process is a clean process and has nearly no emissions or waste. See tyre to oil plant here.